How to speed up cobot integration
Publisert 8. februar 2023 i Operational Excellence
Good planning and strong partners help SMEs overcome hurdles in automation.
Collaborative robots, also known as cobots, are enjoying great popularity because they make it possible to automate time-consuming and resource-intensive tasks. The global market for collaborative robots is currently estimated at around $1.2 billion. The sales volume of cobots reached a total of 32,300 units in 2021. Especially in times when it is becoming increasingly difficult for companies to find and retain suitable employees, such technologies are worth their weight in gold in many places. Speaking of gold, some may ask: Cobots must be extremely expensive, right? When does such an investment pay off?
Automation expert OMRON would like to alleviate such worries, especially for small and medium-sized companies: Smart and integrated robotics solutions as well as cobots and mobile robots are feasible and affordable. For those who want to estimate the return on investment, OMRON’s ROI calculator provides a quick and easy overview.
Cobots and autonomous mobile robots (AMR) are suitable for both SMEs and large-scale businesses. They perform tasks such as transport, palletizing, loading and unloading of machines, assembly, painting, or welding. They can be quickly and flexibly retooled and also programmed by non-experts. Material replenishment can be streamlined with AMRs, and machine and process loading with cobots. However, to successfully carry out such projects and accelerate robot integration, know-how and partners who are familiar with the subject matter are needed. And above all, employees must be informed and involved from the start of the project to be part of the change together.
Here are some tips companies should keep in mind when integrating cobots:

1. Find out where and how robotics can support employees
At the beginning of the automation project, decision-makers and employees must consider together how processes can be made better and more efficient. Some tasks have been performed manually and always in the same way for many years, mostly by employees, without questioning: Does it have to be this way? Could it be done differently and better? Therefore, the beginning of every automation project must start with comprehensive planning, which ideally includes everyone who is involved in current and future processes.
Employees and operators should always be at the center of attention, they should know and learn that robots can support them, while they can devote themselves to other and more interesting tasks. Thanks to cobots, employees are relieved of monotonous, physically demanding, or dangerous work. Examples may include lifting heavy loads, simple pick-and-place applications, parts handling, sorting and palletizing, or work that is hazardous to health. The actual end customer of the cobot technology is not the company per se, but the employee or operator. If he or she is dissatisfied, the cobot investment is doomed from the start. All stakeholders, e.g., the safety department, works council, the operator and IT must be involved in such a project from the very beginning.
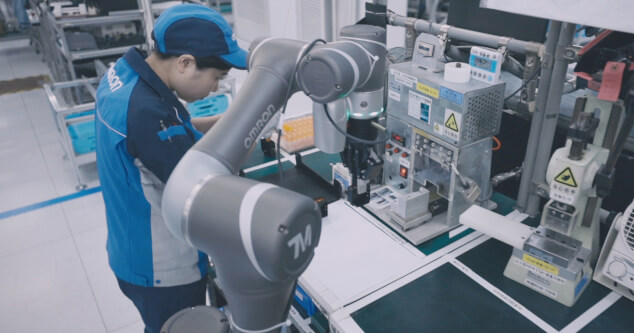